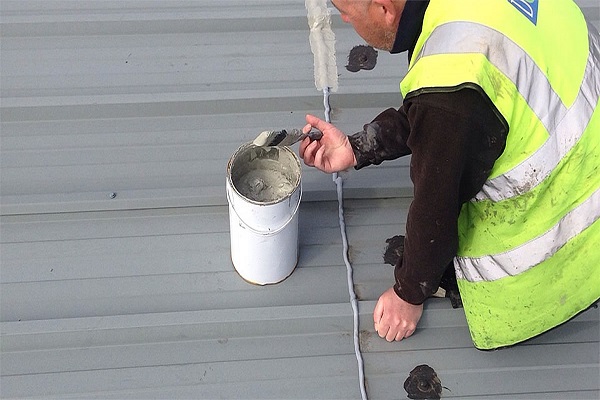
Global Composite Coatings Market has valued at USD1286.35 million in 2022 and is anticipated to project robust growth in the forecast period with a CAGR of 6.47% through 2028. The demand for composite coatings with improved mechanical properties, such as corrosion resistance, abrasion resistance, and wear resistance, is steadily increasing. This can be attributed to the growing utilization of high-performance and lightweight materials across various industries. In particular, the automotive industry extensively relies on composite coatings to enhance vehicle fuel efficiency. The ability of these coatings to reduce weight and improve fuel economy is expected to drive significant market revenue growth in the automotive sector during the forecast period.
Moreover, composite coatings offer superior resistance to wear and tear, thereby extending the lifespan of vehicle parts. This attribute is highly advantageous considering the rising popularity of electric vehicles (EVs), which require lightweight components for optimal performance. As a result, the demand for composite coatings is projected to witness a substantial increase in the EV industry.The aerospace sector is another significant consumer of composite coatings, primarily due to their ability to enhance the performance of aircraft components. These coatings provide increased resistance to corrosion, erosion, and fatigue, effectively prolonging the lifespan of critical aircraft parts.Similarly, the Oil and Gas (O&G) industry extensively utilizes composite coatings to protect pipelines, drilling equipment, and storage tanks against corrosion and abrasion. The exceptional performance offered by these coatings contributes to the overall efficiency and safety of O&G operations.Furthermore, robust revenue growth in the marine sector, coupled with the increasing need for offshore exploration and maritime transport, further drives the expansion of the composite coatings market. The maritime industry heavily relies on composite coatings to provide effective defense against corrosion and fouling, ensuring the longevity and performance of marine structures and vessels.Additionally, the construction field is witnessing a growing requirement for composite coatings to provide exceptional defense against corrosion and weathering. Materials such as steel, concrete, and wood utilized in construction projects greatly benefit from the extended lifespan facilitated by composite coatings’ heightened resistance to rust and weather-related damage.Overall, the demand for composite coatings is expected to continue its upward trajectory across various industries, driven by the need for superior protection, enhanced performance, and extended lifespan of critical components and structures.Key Market DriversGrowing Demand of Composite Coatings in Automotive IndustryThe global composite coatings market has been witnessing significant growth, driven by the growing demand for composite coatings in the automotive industry. Composite coatings offer numerous benefits, such as enhanced durability, improved performance, and increased resistance to corrosion, chemicals, and wear. These advantages have made composite coatings increasingly popular in automotive applications, thus contributing to the expansion of the global market.Composite coatings are specifically designed to enhance the performance and functionality of various automotive components, including exterior body parts, interior trim, engine components, chassis, and suspension systems. These coatings not only provide lightweight yet robust protection but also help improve fuel efficiency and reduce emissions. As the automotive industry continues to prioritize sustainability and fuel economy, the demand for composite coatings has risen.One of the key drivers behind the growing demand for composite coatings in the automotive industry is the need for advanced corrosion protection. Automotive components are exposed to various environmental factors, including moisture, salt, UV radiation, and chemicals. Composite coatings provide a barrier that effectively protects against corrosion, extending the lifespan of automotive parts and reducing maintenance costs. With the rising demand for vehicles in regions with harsh climates, such as coastal areas, the need for effective corrosion protection has become imperative.Moreover, composite coatings offer excellent chemical resistance, making them suitable for automotive components that come into contact with various fluids, fuels, and automotive chemicals. The ability of composite coatings to withstand exposure to these substances without degradation or damage ensures the longevity and reliability of automotive parts, leading to increased adoption in the industry.In addition to protection, composite coatings also contribute to improving the aesthetics of automotive components. These coatings can be customized to achieve various finishes, colors, and textures, thus enhancing the visual appeal of vehicles. With consumers placing importance on the appearance of their cars, automotive manufacturers are increasingly incorporating composite coatings to create sleek, attractive designs.Furthermore, composite coatings play a crucial role in reducing friction and wear in automotive applications. The automotive industry is constantly seeking ways to improve the efficiency and performance of vehicles. Composite coatings with low friction properties are applied to critical components such as engine parts, bearings, and gears, reducing energy loss and enhancing overall vehicle performance. These coatings also minimize wear and tear, leading to increased durability and reliability.The increasing adoption of electric and hybrid vehicles has further fueled the demand for composite coatings in the automotive industry. As these vehicles gain popularity, there is a need for lightweight materials that can help optimize range and battery life. Composite coatings offer a viable solution by providing a lightweight protective layer that ensures the longevity and performance of electric and hybrid vehicle components.In conclusion, the growing demand for composite coatings in the automotive industry is a significant driver of the global composite coatings market. The need for advanced corrosion protection, chemical resistance, improved aesthetics, and enhanced performance in vehicles has propelled the adoption of composite coatings. As automotive manufacturers continue to prioritize sustainability, fuel efficiency, and superior performance, the demand for composite coatings is expected to rise steadily, driving the growth of the global market. With ongoing technological advancements and increasing awareness of the benefits offered by composite coatings, the future of this market looks promising.Growing Demand of Composite Coatings in Oil and Gas IndustryThe global composite coatings market has experienced significant growth, primarily driven by the increasing demand for composite coatings in the oil and gas industry. This expansion can be attributed to the unique properties and benefits offered by composite coatings, making them highly suitable for protecting equipment and infrastructure in the harsh and demanding environments of the oil and gas sector.Composite coatings are specifically designed to provide superior protection against corrosion, abrasion, erosion, and chemical attack. These coatings find extensive applications in various oil and gas equipment, such as pipelines, tanks, valves, offshore structures, and drilling equipment. Given the challenging operating conditions, including exposure to saltwater, corrosive substances, and extreme temperatures, the oil and gas industry requires durable solutions. Composite coatings offer exceptional resistance to these harsh conditions, ensuring the longevity and reliability of the equipment.One of the primary drivers behind the adoption of composite coatings in the oil and gas industry is the need for effective corrosion protection. Corrosion poses a significant challenge, leading to equipment failure, leaks, and increased maintenance costs. By acting as a protective barrier, composite coatings isolate metal surfaces from corrosive agents, significantly extending the lifespan of equipment. Moreover, the use of composite coatings reduces downtime and maintenance expenses, making them an indispensable solution for the oil and gas industry.Furthermore, composite coatings exhibit excellent resistance to abrasion and erosion, both of which are common challenges faced by the oil and gas sector. Equipment such as pumps, valves, and pipelines experience high pressures, flow rates, and the presence of abrasive particles. Composite coatings with enhanced wear resistance can effectively prevent damage to critical components, ensuring reliable operation and minimizing the need for frequent replacements or repairs.In addition to corrosion and wear resistance, composite coatings demonstrate remarkable chemical resistance. Given the wide range of corrosive and aggressive chemicals encountered in the oil and gas industry, including acids, alkalis, and hydrocarbons, the ability of composite coatings to withstand exposure to these chemicals is paramount. The chemical resistance of composite coatings ensures the safe and efficient operation of oil and gas facilities, offering reliable protection to underlying equipment.Moreover, composite coatings offer thermal insulation properties, which are crucial for the oil and gas industry, especially in offshore installations or subsea applications where equipment is exposed to extreme temperatures. By providing thermal insulation, composite coatings minimize heat transfer and mitigate the risk of thermal expansion or contraction. This ability to withstand temperature variations helps maintain the structural integrity and performance of equipment in demanding environments, ensuring optimal operational efficiency.The growing demand for energy and the exploration of new oil and gas reserves have further contributed to the increasing adoption of composite coatings. As the industry expands into more challenging and remote regions, the need for reliable and durable coatings becomes even more critical. Composite coatings provide a cost-effective solution for protecting infrastructure in these harsh environments, ensuring operational efficiency, safety, and sustainability.In conclusion, the escalating demand for composite coatings in the oil and gas industry is driving the growth of the global composite coatings market. The need for superior corrosion protection, wear resistance, chemical resistance, and thermal insulation in the oil and gas sector has led to the widespread adoption of composite coatings. As the industry continues to evolve and faces increasingly demanding challenges, the demand for advanced composite coatings is expected to rise, further fueling the growth of the global market.Download FREE Sample Report @ https://www.techsciresearch.com/sample-report.aspx?cid=2660
Key Market Challenges
Raw Material Availability and Price VolatilityComposite coatings are meticulously formulated using a carefully balanced combination of various raw materials. These materials, including resins, fibers, fillers, additives, and solvents, come together to create coatings with specific properties and performance characteristics. The availability of these raw materials, however, can be influenced by a multitude of factors, making it an intricate puzzle to maintain a steady supply.One of the primary concerns when it comes to raw material availability lies in the dependency on petrochemical-based resins. Many composite coatings heavily rely on resins derived from petroleum products, such as epoxy, polyurethane, and polyester resins. The production of these resins is intricately linked to the availability and price of crude oil and its derivatives. Fluctuations in oil prices or disruptions in the supply chain can significantly impact the availability and cost of these resins, consequently affecting the production and pricing of composite coatings.Beyond the realm of resins, other key raw materials used in composite coatings also face their own set of availability challenges. Fibers, such as carbon fiber and glass fiber, play a crucial role in reinforcing the coatings and imparting strength and durability. However, the production capacity of these fibers is limited, and any disruptions in the supply chain or increased demand from other industries can lead to shortages and price hikes. Similarly, additives and specialty chemicals used in composite coatings may have limited production capacities or face supply chain challenges, further impacting their availability and cost.Moreover, the global market for raw materials used in composite coatings is highly competitive, with multiple industries vying for limited resources. This competitive landscape intensifies the challenges related to raw material availability. Industries such as automotive, aerospace, oil and gas, and construction all require substantial quantities of raw materials for their respective composite coating needs. The demand from these industries can create imbalances in supply and demand, leading to shortages and price volatility.Price volatility is another critical challenge faced by the global composite coatings market due to raw material availability. Fluctuations in raw material prices directly impact the production costs for composite coatings. During periods of shortages or increased demand, raw material prices tend to rise, thereby increasing the production expenses for manufacturers. These increased costs are often passed on to customers, affecting the competitiveness and profitability of the market.In summary, the intricate nature of composite coatings and their raw materials necessitates a deep understanding of the challenges related to raw material availability. By carefully navigating these complexities, the industry can strive to ensure a steady supply of high-quality composite coatings, meeting the diverse needs of various sectors while fostering sustainable growth.
Key Market Trends
Expansion in Aerospace and DefenseThe global composite coatings market is experiencing a substantial trend of expansion, particularly in the aerospace and defense sectors. With continuous growth in these industries, there is a rising demand for advanced coating solutions that provide enhanced protection, durability, and performance. Composite coatings, with their unique properties and characteristics, are increasingly becoming the preferred choice for aerospace and defense applications, thus driving the overall growth of the global composite coatings market.The aerospace industry, encompassing both commercial and military aircraft manufacturing, serves as one of the primary drivers behind the expansion of the global composite coatings market. The demand for lightweight and fuel-efficient aircraft is on the rise, and composite materials play a pivotal role in achieving these objectives. Composite coatings serve as an additional layer of protection for critical aircraft components, including fuselages, wings, and engine parts, ensuring resistance against corrosion, abrasion, and harsh environmental conditions.Composite coatings offer several advantages in aerospace applications. They exhibit excellent mechanical strength, high impact resistance, and fatigue resistance, which are crucial for withstanding the extreme conditions experienced during flight operations. Furthermore, these coatings can be customized to meet specific requirements such as thermal insulation, electromagnetic shielding, and anti-icing properties. As aircraft designs continue to evolve and manufacturers strive for improved performance, composite coatings have become an integral part of ensuring the longevity and reliability of aerospace structures.In the defense sector, composite coatings play a vital role in protecting military equipment and vehicles from hostile environments and combat conditions. Military aircraft, armored vehicles, naval vessels, and missiles require robust coatings that can withstand extreme temperatures, chemical exposure, and physical stress. Composite coatings offer exceptional resistance to corrosion, erosion, and chemical attack, thereby enhancing the durability and longevity of defense equipment in demanding operational environments.Moreover, the expansion of the aerospace and defense industries is not limited to developed economies but is also being witnessed in emerging markets. Countries across the globe are making significant investments in the modernization of their defense capabilities and the development of indigenous aerospace manufacturing capabilities. This increased investment in aerospace and defense infrastructure provides a strong foundation for the growth and development of the global composite coatings market.As the aerospace and defense sectors continue to advance, the demand for innovative composite coatings solutions is expected to further increase. With ongoing advancements in technology and the continuous pursuit of improved performance and efficiency, the global composite coatings market is poised for significant growth in the coming years.
Segmental Insights
Technology InsightsBased on the category of technology, the brazing segment emerged as the dominant player in the global market for Composite Coatings in 2022. The brazing technique, a widely employed method, plays a crucial role in enhancing the toughness of coatings, offering superior resistance. These coatings not only provide excellent waterproofing and corrosion protection but also shield against harmful factors such as UV radiation, scratches, excessive heat, and fire. The lightweight composite coatings market, primarily utilized in the aerospace, automobile, and defense industries, is projected to experience substantial growth in the forthcoming years due to its exceptional properties and applications.End User InsightsThe Aerospace & Defense segment is projected to experience rapid growth during the forecast period. Composite coatings, consisting of a combination of different materials, are gaining significant traction in aerospace and defense applications. This is primarily because of their exceptional attributes, including high strength, lightweight nature, and remarkable resistance to corrosion and wear. However, their impact goes beyond these advantages. The application of composite coatings on crucial aircraft components, such as wings, fuselages, and propellers, not only enhances overall aircraft efficiency, but also contributes to reduced fuel consumption. By leveraging the unique properties of composite coatings, aerospace and defense industries are able to achieve enhanced performance, durability, and sustainability in their operations.Related ReportsCellulose Acetate Market [2028] – Analysis, Trends, & InsightsPersulfates Market [2028]: Trends & ForecastTable of Content-Composite Coatings Market
- Research Methodology
2.1. Objective of the Study2.2. Baseline Methodology2.3. Key Industry Partners2.4. Major Association and Secondary Sources2.5. Forecasting Methodology2.6. Data Triangulation & Validation2.7. Assumptions and Limitations
- Executive Summary
3.1. Overview of the Market3.2. Overview of Key Market Segmentations3.3. Overview of Key Market Players3.4. Overview of Key Regions/Countries3.5. Overview of Market Drivers, Challenges, Trends
- Global Composite Coatings Market: Demand-Supply Analysis
4.1. By Region
- Global Composite Coatings Market Outlook
5.1. Market Size & Forecast5.1.1. By Value5.2. Market Share & Forecast5.2.1. By Technique (Laser Melt Injection, Brazing, Electroless Plating, Others)5.2.2. By Application (Anti-Corrosion, UV Protection, Thermal Protection, Others)5.2.3. By End User (Transportation, Aerospace & Defense, Industrial, Oil & Gas, Others)5.2.4. By Region5.2.5. By Company (2022)5.3. Market Map5.3.1. By Technique5.3.2. By Application5.3.3. By End User5.3.4. By Region
- Asia Pacific Composite Coatings Market Outlook
6.1. Market Size & Forecast6.1.1. By Value6.2. Market Share & Forecast6.2.1. By Technique6.2.2. By Application6.2.3. By End User6.2.4. By Country6.3. Asia Pacific: Country Analysis6.3.1. China Composite Coatings Market Outlook6.3.1.1. Market Size & Forecast6.3.1.1.1. By Value6.3.1.2. Market Share & Forecast6.3.1.2.1. By Technique6.3.1.2.2. By Application6.3.1.2.3. By End User6.3.2. India Composite Coatings Market Outlook6.3.2.1. Market Size & Forecast6.3.2.1.1. By Value6.3.2.2. Market Share & Forecast6.3.2.2.1. By Technique6.3.2.2.2. By Application6.3.2.2.3. By End User6.3.3. Australia Composite Coatings Market Outlook6.3.3.1. Market Size & Forecast6.3.3.1.1. By Value6.3.3.2. Market Share & Forecast6.3.3.2.1. By Technique6.3.3.2.2. By Application6.3.3.2.3. By End User6.3.4. Japan Composite Coatings Market Outlook6.3.4.1. Market Size & Forecast6.3.4.1.1. By Value6.3.4.2. Market Share & Forecast6.3.4.2.1. By Technique6.3.4.2.2. By Application6.3.4.2.3. By End User6.3.5. South Korea Composite Coatings Market Outlook6.3.5.1. Market Size & Forecast6.3.5.1.1. By Value6.3.5.2. Market Share & Forecast6.3.5.2.1. By Technique6.3.5.2.2. By Application6.3.5.2.3. By End User
- Europe Composite Coatings Market Outlook
7.1. Market Size & Forecast7.1.1. By Value7.2. Market Share & Forecast7.2.1. By Technique7.2.2. By Application7.2.3. By End User7.2.4. By Country7.3. Europe: Country Analysis7.3.1. France Composite Coatings Market Outlook7.3.1.1. Market Size & Forecast7.3.1.1.1. By Value7.3.1.2. Market Share & Forecast7.3.1.2.1. By Technique7.3.1.2.2. By Application7.3.1.2.3. By End User7.3.2. Germany Composite Coatings Market Outlook7.3.2.1. Market Size & Forecast7.3.2.1.1. By Value7.3.2.2. Market Share & Forecast7.3.2.2.1. By Technique7.3.2.2.2. By Application7.3.2.2.3. By End User7.3.3. Spain Composite Coatings Market Outlook7.3.3.1. Market Size & Forecast7.3.3.1.1. By Value7.3.3.2. Market Share & Forecast7.3.3.2.1. By Technique7.3.3.2.2. By Application7.3.3.2.3. By End User7.3.4. Italy Composite Coatings Market Outlook7.3.4.1. Market Size & Forecast7.3.4.1.1. By Value7.3.4.2. Market Share & Forecast7.3.4.2.1. By Technique7.3.4.2.2. By Application7.3.4.2.3. By End User7.3.5. United Kingdom Composite Coatings Market Outlook7.3.5.1. Market Size & Forecast7.3.5.1.1. By Value7.3.5.2. Market Share & Forecast7.3.5.2.1. By Technique7.3.5.2.2. By Application7.3.5.2.3. By End User
- North America Composite Coatings Market Outlook
8.1. Market Size & Forecast8.1.1. By Value8.2. Market Share & Forecast8.2.1. By Technique8.2.2. By Application8.2.3. By End User8.2.4. By Country8.3. North America: Country Analysis8.3.1. United States Composite Coatings Market Outlook8.3.1.1. Market Size & Forecast8.3.1.1.1. By Value8.3.1.2. Market Share & Forecast8.3.1.2.1. By Technique8.3.1.2.2. By Application8.3.1.2.3. By End User8.3.2. Mexico Composite Coatings Market Outlook8.3.2.1. Market Size & Forecast8.3.2.1.1. By Value8.3.2.2. Market Share & Forecast8.3.2.2.1. By Technique8.3.2.2.2. By Application8.3.2.2.3. By End User8.3.3. Canada Composite Coatings Market Outlook8.3.3.1. Market Size & Forecast8.3.3.1.1. By Value8.3.3.2. Market Share & Forecast8.3.3.2.1. By Technique8.3.3.2.2. By Application8.3.3.2.3. By End User